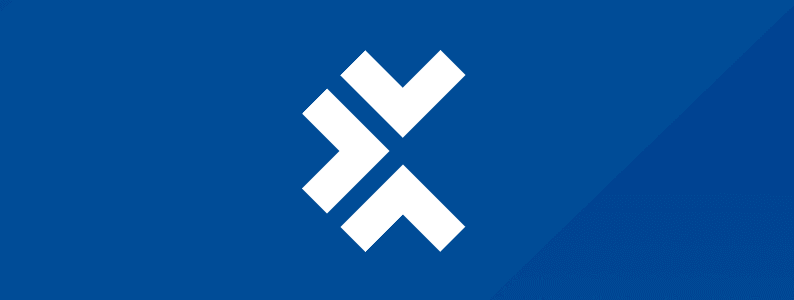
What are GAMP guidelines?
GAMP is a technical committee that was established under the International Society for Pharmaceutical Engineering (ISPE). The primary goal of the GAMP committee is to promote the regulation of automated systems within the pharmaceutical industry.
GAMP guidelines are used by manufacturers and users to maintain operational efficiency and ensure that drugs or food products have the best quality. It allows companies to perform quality testing at every stage of the development process as well as cross-check facilities, equipment, materials, operator hygiene, etc.
There are GAMP Good Practice Guides on specific automated processes such as calibration management, records and data integrity, electronic data archiving, mobile applications, manufacturing execution systems, process control, IT infrastructure control and compliance, system testing, etc.
GAMP was founded in 1991 in United Kingdom to improve the understanding of the evolving expectations of regulatory agencies.
What is the history of GAMP?
GAMP was founded in 1991 in the United Kingdom to improve the understanding of the evolving expectations of regulatory agencies. It prepares the pharmaceutical industry for GAMP compliance of manufacturing systems.
GAMP has published significant guidance documents for the validation of automated systems in pharmaceutical manufacturing. From 1994 to 2022, GAMP produced supplier guides, risk analysis, risk assessment, and risk management approach guides. The latest guidance document available is the GAMP 5 second edition.
Why is GAMP important?
GAMP seeks to improve understanding of how computer systems should be validated in pharmaceutical and other related industries. Let’s discuss a few reasons why GAMP guidance is considered to be very important.
Compliance
GAMP helps regulated companies adhere to the regulatory requirements for pharmaceutical and other product manufacturing industries. It ensures compliance with industry standards and computer systems regulations.
Quality and safety
GAMP helps to improve the quality and safety measures utilized in automated manufacturing processes. GAMP Good Practice Guides help reduce deviations and defects in order to boost overall product quality and patient safety.
Risk mitigation
GAMP promotes the use of risk management strategies during the systems development life cycle. Without doubt, it allows suppliers and users to identify as well as prevent common risks such as data integrity issues, software glitches, equipment failures, etc.
Process efficiency
GAMP helps to streamline automation systems and optimize workflows in order to enhance manufacturing efficiency. It encourages organizations to follow standardized procedures, documentation best practices, and computerized system validation.
Data integrity
GAMP emphasizes data integrity practices to guarantee accurate and reliable manufacturing data records. It ensures that companies can analyze and spearhead reporting, ascertain critical information, and therefore, make improved decisions.
Continuous improvement
GAMP encourages life cycle approaches when tackling system development, maintenance, and implementation. The guidelines advocate for continuous assessment and improvement of computerized manufacturing systems.
GAMP provides comprehensive guidelines for ensuring that computerized systems in pharmaceutical manufacturing are compliant, reliable, and of the highest possible quality.
What is GAMP 5?
Good Automated Manufacturing Practice is focused on developing cost-effective frameworks for good practices with automated manufacturing systems. It ensures that computerized systems are effective, suitable for intended use, and readily compliant. Over the years, GAMP has produced exemplary guidance documents for this sole purpose.
The current guidance document from ISPE is the GAMP 5, which was initially created in 2008, but a second edition was released in July 2022. The first edition was made to serve as a risk-based approach to ensuring compliant GxP computerized systems. While the newer edition maintains the same principles and framework, there have been some important additions.
The GAMP 5 guide explains how to apply risk management principles and tools, use automated software systems, and build stable connections with service providers. The second edition also emphasizes the need for critical thinking when applying these principles and promotes agile methodology in software development. It’s important to note that GAMP 5 isn’t a standard but aims to provide necessary guidance for meeting industry standards.
Benefits of using GAMP 5
GAMP 5 advises that computer systems should be evaluated and categorized based on their intended use and complexity. This technique is conveniently similar to the V-model in software development, which uses the system testing process to verify specifications and requirements. Let’s see a few benefits of using the GAMP 5 approach below.
Risk reduction
The framework contained in GAMP 5 is meant to lower risks associated with automated manufacturing processes and products. It provides an extensive approach for computer system validation as accepted within the pharmaceutical and related industries.
Global compliance
GAMP 5 outlines the compliance regulations from the US Food and Drug Administration (FDA) and the European Medicines Agency (EMA). It helps regulated companies to match the crucial expectations for 21 CFR Part 11, Annex 11, and also computerized system validation (CSV).
System testing
GAMP 5 promotes a risk-based approach to system testing to ensure that companies focus mostly on high-risk areas of the system. Likewise, it also uses testing to validate the automated system efficiently and confirm that it works as intended.
Reference materials
The GAMP Good Practice Guides are available to support companies who follow the GAMP 5 risk-based approach. Furthermore, the reference materials convey best practices for automation in conjunction with useful tips for performing the validation of different systems.
Standards compatibility
GAMP 5 was created to meet the evolving FDA expectations for GMP compliance of manufacturing and related systems. It’s also compatible with international standards such as IEEE standards, ISO 9000, ISO 12207, IT Infrastructure Library (ITIL), and others.
Agile
The GAMP 5 second edition embraces a dynamic and flexible approach since today’s software and cloud-enabled applications demand continuous improvements. It recommends the agile methodology since it allows for the use of an iterative, incremental, and exploratory approach.
Critical thinking
Both the GAMP5 second edition and the FDA’s guidelines from September 2022 emphasize how critical thinking helps to ensure the integrity of computerized systems. The new GAMP edition promotes a more efficient and risk-based approach tailored to the software’s unique risk profile. It also enhances the focus on critical thinking, offers clear guidance on where to apply it, and dedicates a new appendix to the topic of critical thinking to enrich the document’s content.
What are the main components and uses of GAMP?
GAMP provides comprehensive guidelines for ensuring that computerized systems in pharmaceutical manufacturing are compliant, reliable, and of the highest possible quality. GAMP principles and components allow companies to adhere to regulatory requirements. Below are the main components and uses of GAMP.
GAMP provides comprehensive guidelines for ensuring that computerized systems in pharmaceutical manufacturing are compliant, reliable, and of the highest possible quality.
GAMP guidance
GAMP provides guidelines and best practices for the development and implementation of automated systems in the manufacturing industry. It highlights the expectations and approaches for achieving system compliance.
Risk management
GAMP emphasizes the importance of risk management when working with automated systems. It allows companies to be attentive to their automated processes, equipment, and software in order to swiftly identify potential risks.
Validation
Validation is an important component of GAMP that demonstrates how to confirm that automated software systems match the requirements and operate as intended. It helps with validation strategies as well as industry standards criteria.
System Development Life Cycle (SDLC)
GAMP is concerned with system development and seeks to help organizations use a life cycle approach to develop automated systems. It states that all system development stages are properly planned, regulated, and validated.
Supplier and vendor management
GAMP also realizes that vendors and suppliers are a crucial part of automated systems development and integration. They have provided guidelines to help organizations choose software vendors that meet necessary regulatory requirements.
Change control and configuration management
Computerized systems that are being supplied and used in the pharmaceutical industry also need to go through change control and configuration management. This means that system upgrades, patches, and modifications should be done without compromising integrity.
Some challenges that come with implementing GAMP
GAMP applies to pharmaceuticals, food and beverage, biotech, and medical devices industries. Some challenges may come with implementing GAMP; however, these are often specific to industry, organization size, and the complexity of automated manufacturing processes. Here are some challenges.
Understanding and applying GAMP principles
GAMP principles, best practices, and guidance documents can be somewhat complex. They require an in-depth understanding to interpret and apply to specific manufacturing processes.
Resource allocation
One main challenge of implementing GAMP includes the number of resources required. Moreover, it often expects organizations to dedicate time, personnel, and finances to ensure its success.
Regulatory compliance
The stipulated regulatory requirements given by agencies such as the FDA or EMA can be very demanding. This means that there’s literally so much to do from documentation to validation to verification.
System complexity
Manufacturing processes need complex systems to perform intensive tasks. There’s a possibility of encountering challenges when adhering to GAMP guides and at the same time trying to integrate and validate these automated systems.
Vendor management
It may be difficult to maintain GAMP guidelines and regulatory standards when organizations work with multiple vendors for software, equipment, and automated system integration.
Maintenance and support
GAMP-compliant systems require ongoing maintenance and support in order to ensure quality and effectiveness. This may be a challenge for companies with limited internal resources.
Conclusion
Good Automated Manufacturing Practice is an important factor for developing, implementing, and maintaining computerized systems in manufacturing. For help with enabling compliance with 21 CFR Part 11 and other related regulations, request a demo of the Tricentis Vera™ digital validation tool. To summarize, GAMP components such as validation, supplier management, risk management, and others help to ensure regulation compliance and improve manufacturing product quality in addition to optimizing overall operational efficiency.
This post was written by Susan Ogidan. Susan is a technical content writer who loves to explore developer-facing tools and share valuable insights on them. Susan is an entry-level full-stack developer who strongly believes in the power of code.