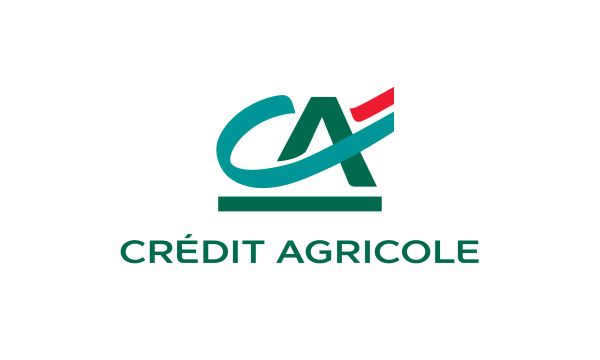
Crédit Agricole Group (CA-GIP) ensures top-notch infrastructure performance with Tricentis NeoLoad
See how Crédit Agricole minimized production incidents by over 30% and improved the overall quality of its applications with Tricentis NeoLoad.
automation of GxP test cases
default
faster test cycle times
default
days shorter release timelines
default
Boehringer Ingelheim has implemented an innovative approach to automated testing to deliver updates to mission-critical software with higher quality and greater speed. In an industry first, a cross-functional team enabled the delivery of updates to its CRM platform through a continuous delivery pipeline – which the organization relies on to engage customers across the world.
With more than 52,000 employees worldwide and sales of over 20 billion Euro in 2021, Boehringer Ingelheim is a leading research-driven biopharmaceutical company. The organization’s focus on innovation in technology plays no small part in that success.
Recently, the IT team embarked on an ambitious project to implement fully automated software delivery so that new features could be delivered to business users – and value could be delivered to customers – in record time. One of the greatest challenges would prove to be automating testing for Veeva CRM, a business-critical system used by 20,000 Boehringer Ingelheim employees. Few in the industry have attempted to automate testing for a GxP regulated application.
See how Crédit Agricole minimized production incidents by over 30% and improved the overall quality of its applications with Tricentis NeoLoad.
Sansiri used Tricentis Tosca to boost SAP test automation, saving...
Learn how a global beauty leader cut test authoring time by 95% and...
A top data storage company automated 465 Oracle ERP test cases with...
Learn how a global gaming company achieved 80% faster releases and...